La sfida Net Zero per l’acciaio green
Dalla riduzione delle emissioni grazie ai forni elettrici al polimero proveniente dalla plastica riciclata al posto del polverino di carbone fino all’ipotizzato impiego dell’idrogeno e oltre: ecco le vie dell’acciaieria italiana
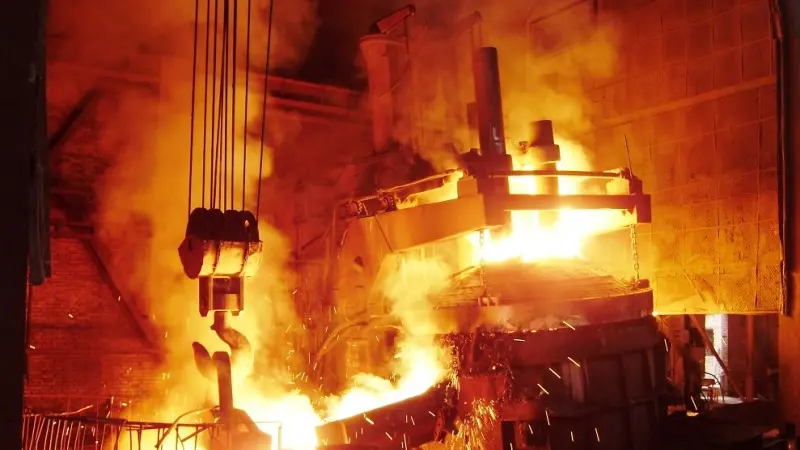
PADOVA. Dalla brown alla green economy anche per la siderurgia. Quello dell’acciaio è infatti uno dei settori considerati tra i maggiori produttori di emissioni di difficile abbattimento. Ed è quindi tra quelli in cui si dovranno fare gli sforzi maggiori per contribuire all’obiettivo zero emissioni di CO2 e altri gas serra entro metà secolo indicato nell’intesa di massima raggiunta, a fatica, al termine del G20 di Roma.
G20 e COP26
L’impegno in campo ambientale dei grandi della Terra per la neutralità carbonica si accompagna al tetto di 1,5 gradi di aumento del riscaldamento globale, allo stop a breve dei finanziamenti pubblici internazionali per nuove centrali a carbone, allo stanziamento di 100 miliardi di dollari l’anno fino al 2025 per i Paesi in via di sviluppo che soffrono particolari impatti del cambiamento climatico.
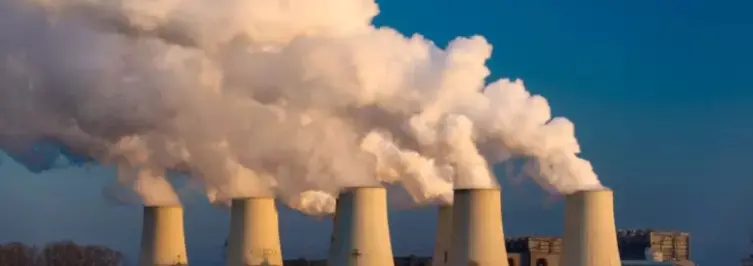
In attesa di verificare alla conferenza ONU COP26, che si è nel frattempo aperta a Glasgow, se in questo senso esiste un’effettiva volontà condivisa a livello internazionale di perseguire nei prossimi anni decise politiche di transizione energetica che vincolino tutti i Paesi, o almeno i maggiori produttori mondiali di emissioni in atmosfera.
Anche se a tal proposito va sottolineato che quando si parla di emissioni zero e di neutralità carbonica, si intende in realtà “emissioni nette zero”. Cioè una condizione in cui per ogni tonnellata di CO2 o altri gas serra diffusi nell’atmosfera, se ne rimuove altrettanta. Quindi l’obiettivo della neutralità carbonica si raggiungerà quando si smetterà di immettere gas serra nell’atmosfera oltre la quantità che si riesce a togliere.
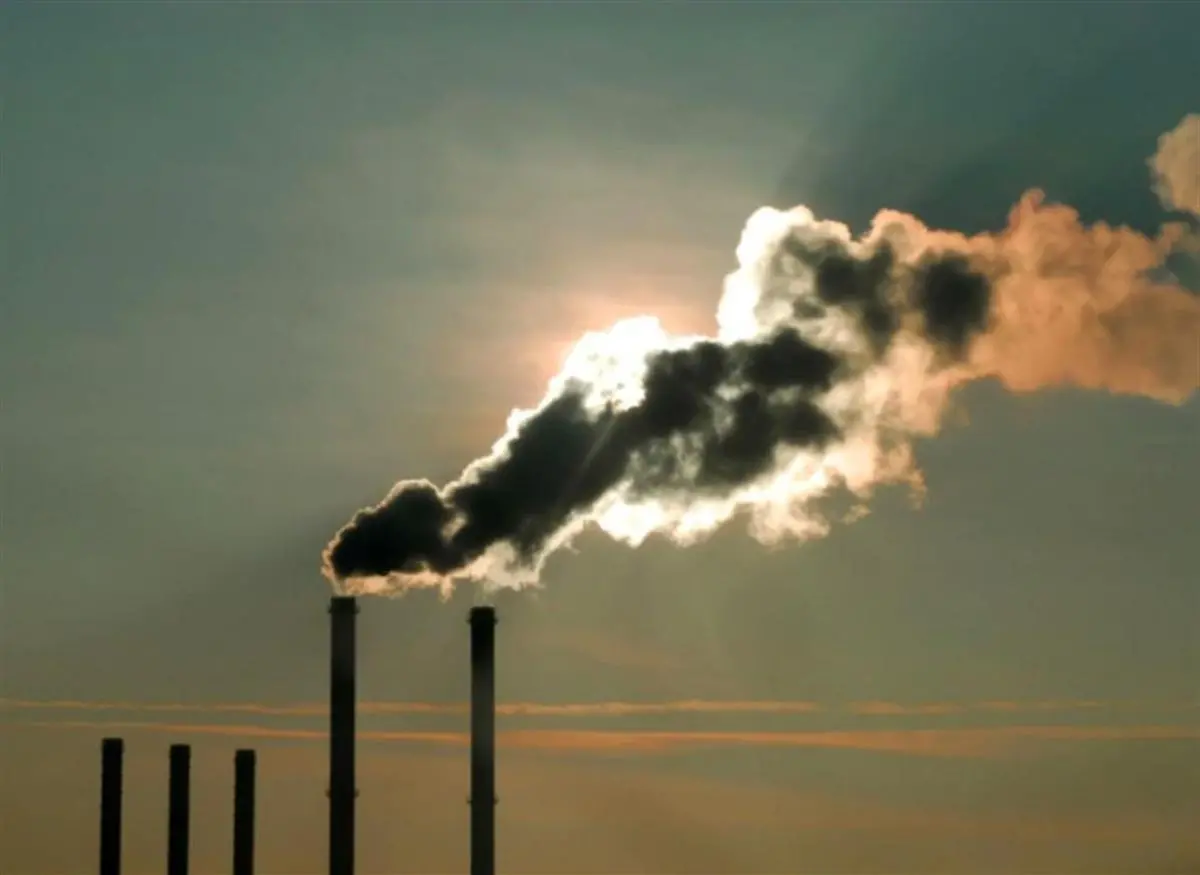
Il mix di soluzioni per i settori Hard to Abate
La sfida più grande in materia ambientale per le industrie energivore ad alto impatto di emissioni è quella di intervenire con una combinazione di soluzioni, su cui occorre però lavorare ancora molto in termini di ricerca scientifica, sviluppo tecnologico e sostenibilità economica per i comparti interessati.
Secondo lo studio “Strategia per la Decarbonizzazione dei settori cosiddetti Hard to Abate” (acciaio, chimica, ceramica, carta, vetro, cemento, fonderie), redatto da Interconnector Energy Italia, Federbeton, Federacciai, Assocarta, Confindustria Ceramica, Federchimica, Assofond e Assovetro in collaborazione con Boston Consulting Group, sono tre gli elementi su cui puntare maggiormente: cattura della CO2, green fuels (idrogeno e biometano), elettrificazione. La loro combinazione potrebbe garantire nel 2050 una riduzione fino al 70-80% delle emissioni totali in questi comparti, mentre un’ulteriore diminuzione del 15-20% verrebbe da altre attività quali efficienza energetica, economia circolare e combustibili low carbon.
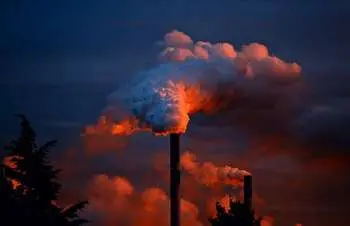
Riduzione delle emissioni nella siderurgia: il progetto Bluair
Nella direzione della decarbonizzazione del settore dell’acciaio si situa certamente il recente avvio in Friuli del nuovo impianto di I.Blu - Gruppo Iren per la produzione, dal riciclo di plastiche miste, del polimero Bluair per l’industria siderurgica.
Un sistema innovativo, unico nel suo genere in Italia, che come agente riducente nel processo siderurgico sostituisce al carbone un polimero ottenuto da plastica riciclata. Una tecnologia che lega effettivamente due attività virtuose, con una ricaduta diretta immediata in termini di applicazione industriale visto l’interesse e l’utilizzo già in essere di questa innovazione da parte di vari player dell’acciaio come Voest Alpine, Feralpi, Abs e Pittini.
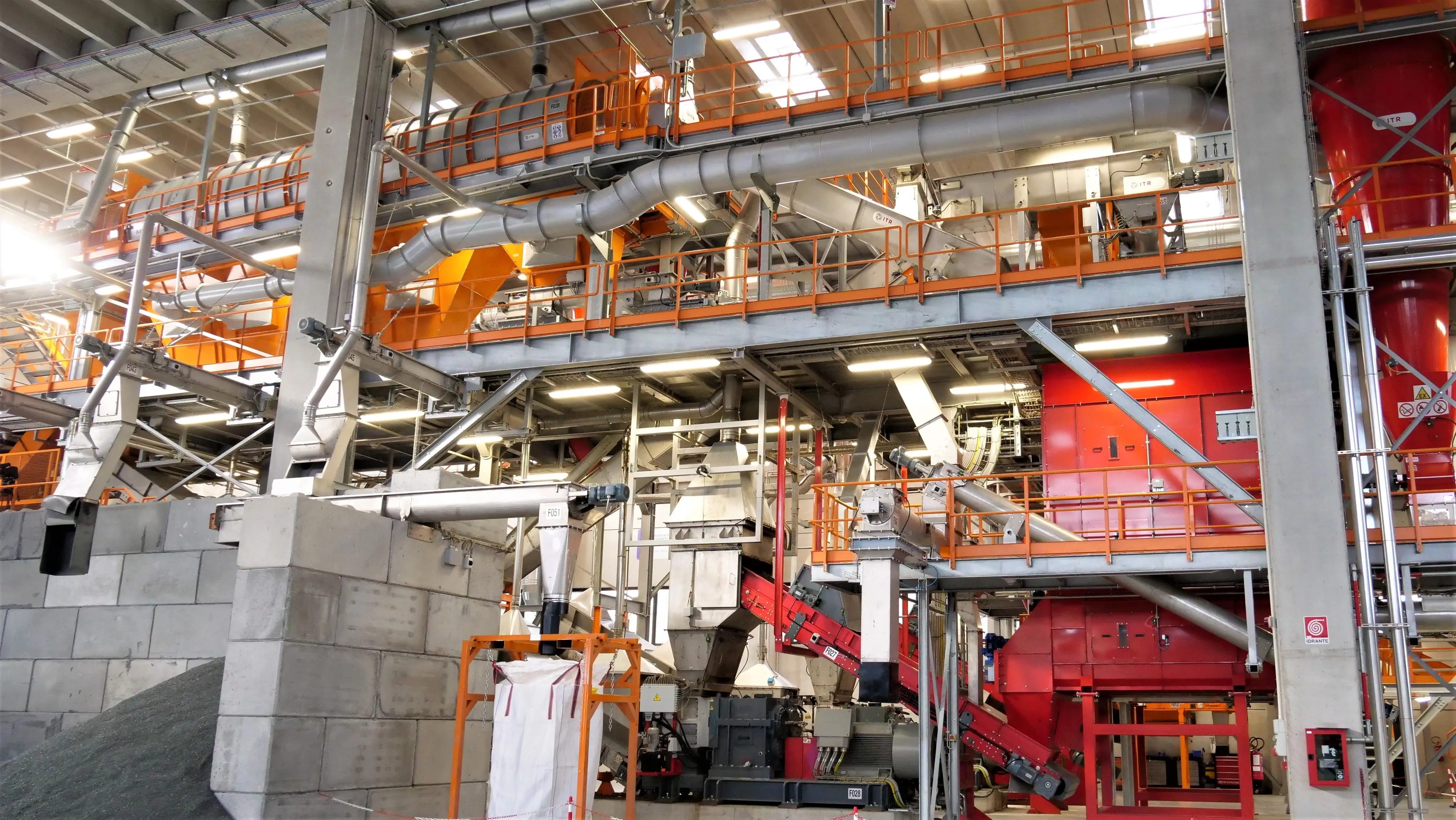
«Bluair consente un miglioramento sia delle performance ambientali dell’industria siderurgica grazie a una riduzione delle emissioni di CO2 superiore al 30%, sia delle prestazioni tecniche: riduce il Tap to Tap Time, contribuisce a ridurre il consumo energetico e dal punto di vista economico consente per ogni tonnellata utilizzata di ridurre gli ETS in rapporto di 1 a 1,1», ha evidenziato l’amministratore delegato di I.Blu Roberto Conte in una recente intervista a Siderweb.com, il quotidiano on line di informazione economica-siderurgica della community italiana dell’acciaio.
L’elettrificazione
Oggi il contesto globale della siderurgia vede già in corso la tendenza ad abbandonare il ciclo integrale per la produzione dell’acciaio, basato sull’uso del carbone, e passare a quello con forno elettrico basato sul riciclo dei rottami ferrosi. Spiega il professore Carlo Mapelli del Dipartimento di Meccanica del Politecnico di Milano: «L’altoforno emette 2,5 tonnellate di anidride carbonica per tonnellata di acciaio, il forno elettrico 0,1/0,2 tonnellate. Cui vanno aggiunte le emissioni di 0,83 tonnellate per tonnellata di acciaio generate dalla soluzione che ovvia all’inquinamento metallurgico dei rottami: l’uso del pre-ridotto, prodotto a partire dal gas naturale. Quantità che potrebbe ridursi a 0,3 tonnellate se si usasse l’idrogeno al posto del gas naturale».
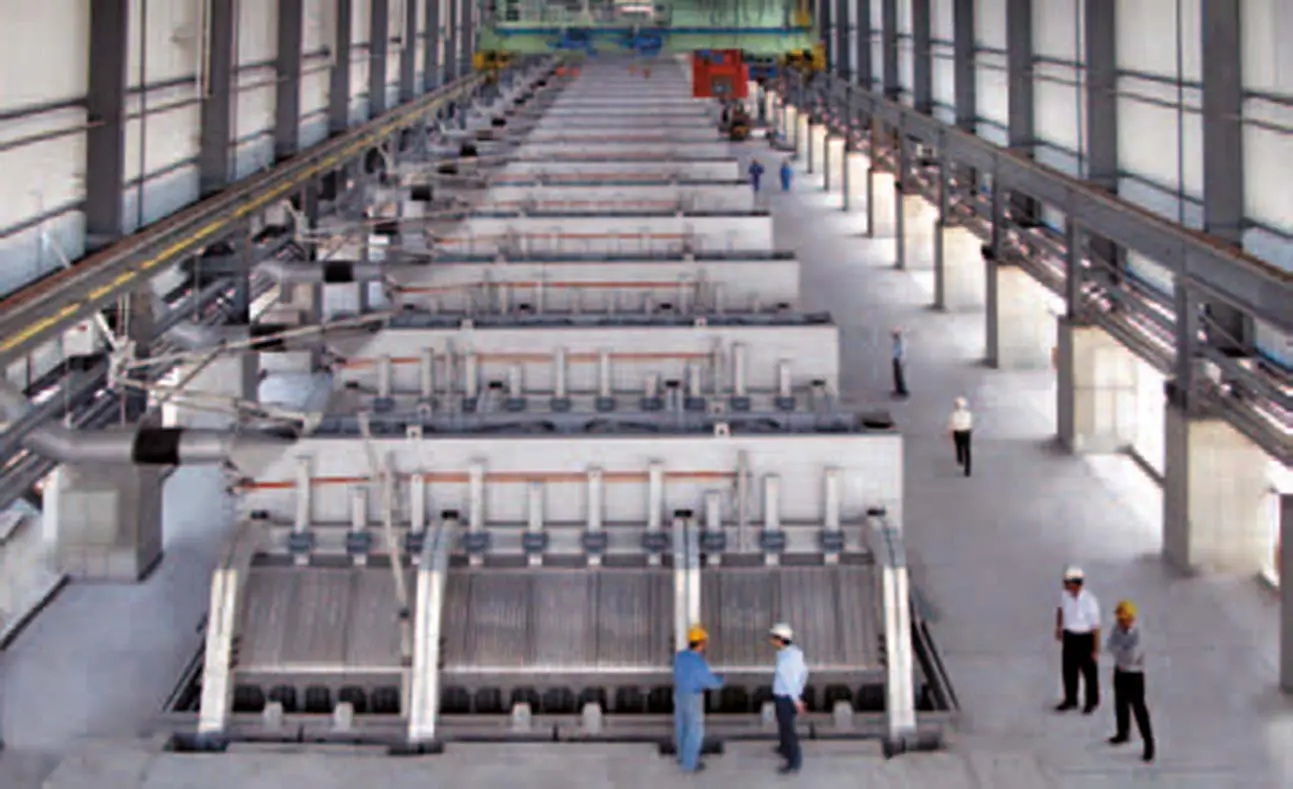
L’idrogeno
Ma secondo Mapelli l’idrogeno non è la soluzione migliore. Neanche quello verde, ottenuto dall’acqua dolce con elettrolizzatori e uso di energia elettrica da fonti rinnovabili come eolico e solare, «che può essere un’ottima fonte di accumulo dell’energia, ma non sarà la svolta». Perché, ha spiegato il professore nel webinar di Siderweb “Cieli azzurri per la siderurgia”, «non è poi così verde in termini di consumo di energia elettrica, di acque e di suolo, e non è competitivo. Per produrne 1 m3 servono 4,64 kWh. Poi ci sono i costi rilevanti degli elettrolizzatori, che potranno diventare competitivi solo se diminuiranno di 5-6 volte rispetto all’attuale. Non è neanche così facile da trasportare, avendo una reattività molto elevata; dovrebbero essere cambiati i tubi e il valvolame degli attuali gasdotti».
Bocciato a maggior ragione l’idrogeno grigio, prodotto da combustibili fossili compreso il carbone, a cui «quindi non possiamo fare riferimento per decarbonizzare». E rimandato con poche speranze di superare l’esame anche l’idrogeno blu da scissione del gas naturale con sequestro della CO2. «Può essere una via interessante, ma non ha molto senso a livello siderurgico: per quale ragione dovrei rinunciare al potenziale riducente ed energetico che è presente nel carbonio che mi sta veicolando il gas naturale? Conviene usare il gas naturale e poi sequestrare la CO2 che ho realizzato».
Sulla questione dell’effettiva sostenibilità economica dell’utilizzo dell’idrogeno su larga scala concorda Giuseppe Ferrario, esperto consulente industriale nel settore siderurgico: «Non c’è dubbio che per la decarbonizzazione del processo di produzione dell’acciaio l’idrogeno si presenta come il riducente ideale. Ma la produzione di DRI (ferro pre-ridotto) utilizzando idrogeno invece di gas naturale, seppure già teoricamente possibile, si scontra con l’attuale disponibilità di idrogeno in quantità sufficienti e a costi competitivi”. Secondo Ferrario la strada maestra è quella di passare gradualmente la produzione del ciclo integrale da altoforno e convertitore in riduzione diretta e forno elettrico.
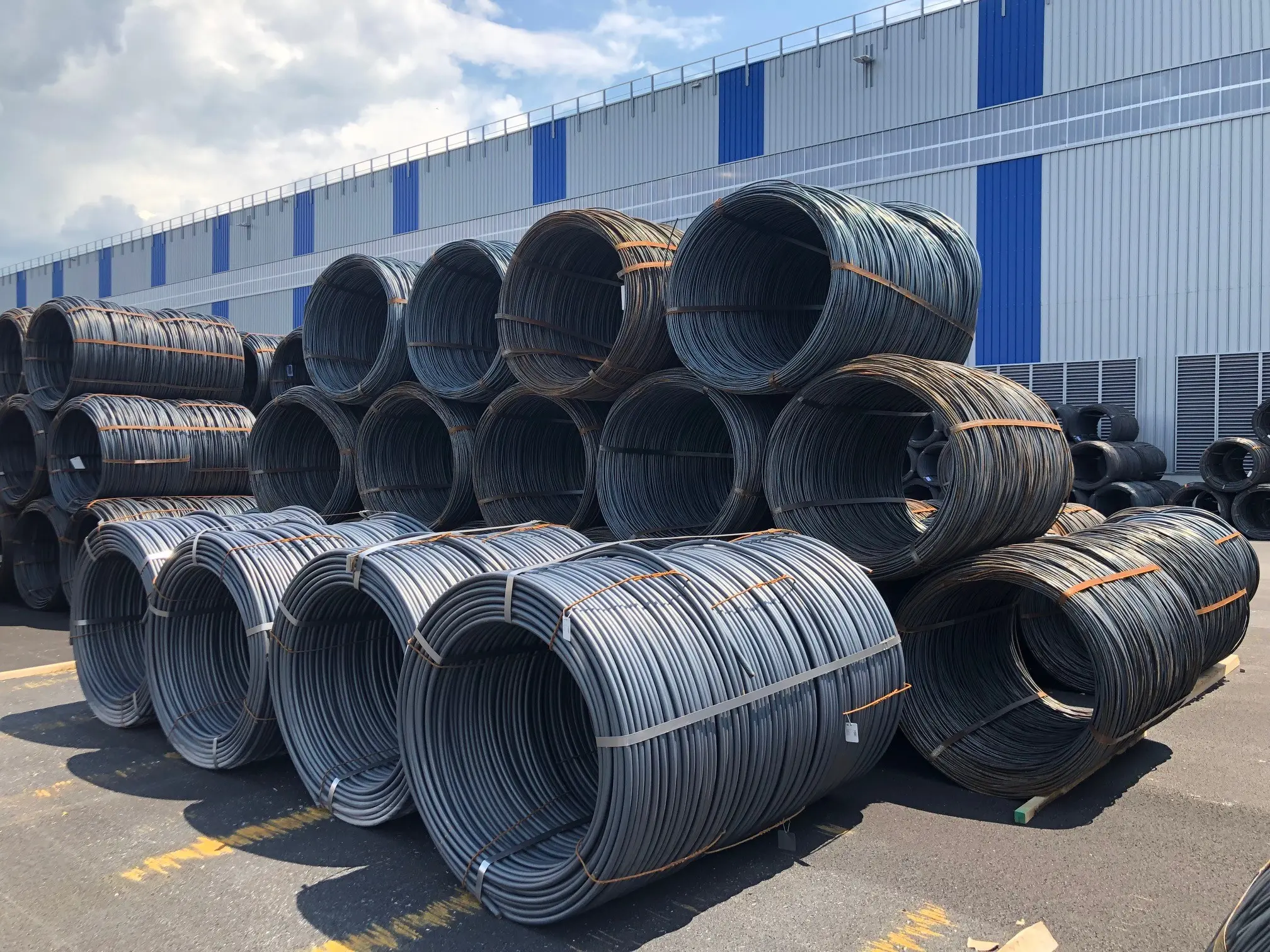
«In una prima fase riduzione diretta alimentata a gas naturale con captazione della CO2, introducendo via via (con il crescere della disponibilità di idrogeno a costi competitivi) quote maggiori di idrogeno al posto del gas naturale». Purché l’idrogeno sia prodotto con fonti energetiche rinnovabili. Poiché «sia la produzione di idrogeno per elettrolisi sia l’utilizzo dei forni elettrici al posto dei convertitori richiedono ingenti quantità di energia elettrica - precisa Ferrario - è importante che queste quantità aggiuntive siano assicurate da fonti rinnovabili o che comunque non generino produzione di CO2, altrimenti rientra dalla finestra quello che abbiamo fatto uscire dalla porta».
La cattura della CO2
Secondo il professor Mapelli una strada migliore per ridurre ed eliminare le emissioni nel ciclo produttivo siderurgico è quella delle soluzioni che puntano al sequestro della CO2 prodotta dalla combustione del gas naturale.
«Gli impianti ad ammine e ad ammoniaca raffreddata sono simili: il flusso di anidride carbonica viene sequestrato dalle ammine e dall’ammoniaca. Da queste miscele viene poi estratto e, in forma pura, può essere convogliato altrove: a stoccaggio, nei depositi sottomarini; a mineralizzare, cioè a formare carbonati a partire da ossidi. Poi ci sono i liquidi ionici: in essi viene trattenuta l’anidride carbonica, che può essere poi separata da una cella elettrolitica e usata per produrre materie prime interessanti, come grafite, grafene o addirittura i nanotubi di carbonio». Una soluzione che Mapelli ritiene migliore dell’idrogeno perché a costi inferiori permette di ottenere il carbonio, di cui si compone con il ferro la lega dell’acciaio, che nel peggiore dei casi costituisce una fonte di accumulo di energia che non viene dispersa nell’atmosfera.
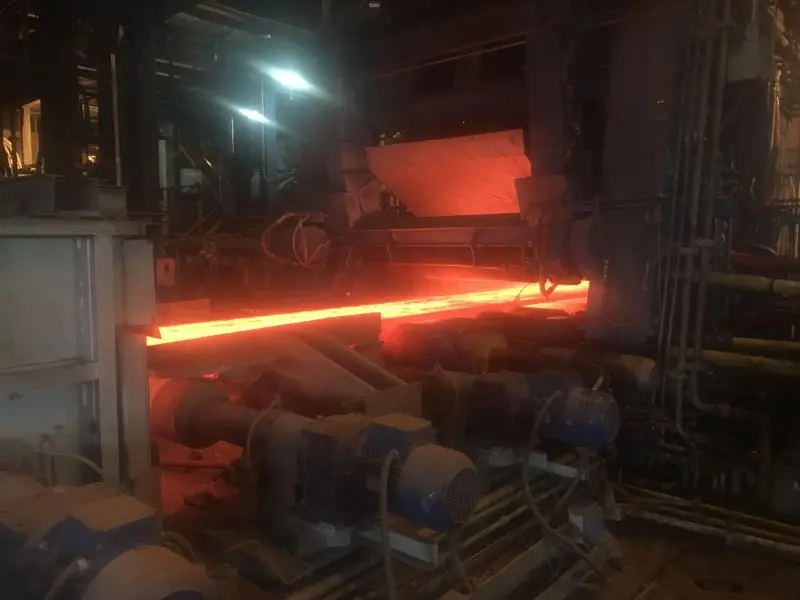
Le biotecnologie
Da percorrere anche la via biotecnologica, con il carbonio di origine biologica. In questo campo Mapelli ha ricordato la sperimentazione della produzione di idrocarburi attraverso batteri che ArcelorMittal sta portando avanti in Belgio, che però non si è ancora consolidata in siderurgia «perché purtroppo questi batteri subiscono degli shock nel momento in cui ci sono delle variazioni nei gas siderurgici, a causa delle concentrazioni di zolfo», e anche l’utilizzo di alghe spiruline.
E poi biocarbone e biometano per ottenere nuovo carbone e gas utilizzati tradizionalmente nel ciclo siderurgico. «Non è uguale al coke (ha resistenze meccaniche diverse) – ha sottolineato Mapelli -, ma ci sono sperimentazioni in cui si usa il biocarbone come elemento riducente». Una soluzione da perseguire anche perché, secondo la normativa europea, «se il biometano e il biocarbone vengono prodotti da scarti agricoli e di allevamento, senza sottrarre suolo alla produzione alimentare, le emissioni di CO2 alla produzione e al consumo non vanno computate tra le emissioni nette, perché si suppone che nel ciclo stagionale le coltivazioni e le risorse boschive saranno in grado di riassorbire carbonio».
Riproduzione riservata © il Nord Est